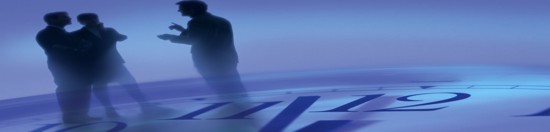
Consulting: Process Transformation:: Six Sigma
Six Sigma is a business management strategy originally developed by Motorola, USA in 1981. As of today, it enjoys widespread application in many sectors of industry, although its application is not without controversy.
Six Sigma seeks to improve the quality of process outputs by identifying and removing the causes of defects (errors) and minimizing variability in manufacturing and business processes. It uses a set of quality management methods, including statistical methods, and creates a special infrastructure of people within the organization ("Black Belts", "Green Belts", etc.) who are experts in these methods.
What is Six Sigma and Why do Companies Need it?
Generally speaking, companies use Six Sigma to reduce variation in products and processes - but the net effect of any Six Sigma project is what people are really looking for: fewer defects, shorter cycle times, increased capacity and throughput, lower costs, higher revenues and reduced capital expenditures.
When Six Sigma is deployed successfuly, systematically and pervasively - with the right technology support and leadership force - it can produce large amounts of cash for shorter-term profitability or for longer-term investments.
The Six Sigma Method - DMAIC
Most people are familiar with the methodological expression of Six Sigma, DMAIC - Define, Measure, Analyze, Improve and Control. Some companies add a R for "recognize" in front of Define and an R for "realize" after Control. You first have to Recognize you have a problem before defining it and, after implementing a solution you have to control it over time to Realize its financial benefits.
While Six Sigma follows the DMAIC methodology at the project level, it follows a well established deployment methodology at the business level. Companies like GE and DuPont have paved the way for making Six Sigma deployable through large networks of Champions, Black Belts, Green Belts, Yellow Belts and Process Owners.
Six Sigma and Total Performance Excellence
In the context of Total Performance Excellence (TPE), Six Sigma focuses more on quality and problem-solving - while Process Management focuses on basic process definition, Lean focuses on time and flow, and Design for Six Sigma focuses on designing new processes or products.