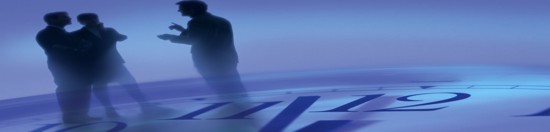
Consulting: Process Transformation:: Lean Manufacturing & Lean Six Sigma
Lean and Lean Six Sigma are a set of methods companies can apply to any manufacturing, transactional or service process to reduce waste, eliminate non-value-added actions and cut time.
Lean methods have a rich and proven history that began in the automobile industry at Ford in the 1920s in a rudimentary way, and at Toyota in the 1950s in a more advanced way. Combining Lean with Six Sigma can produce a program that brings both short-term results - through the power of Lean - and long-term change through the power of Six Sigma. It is for this reason many companies are turning to a combined Lean and Six Sigma effort.
Trimming waste, maximizing margins
IQPM combined Lean and Six Sigma programs are designed to incorporate the best of both methodologies, but Lean continues to have its own unique principles, tools, and even practitioners.
Who Uses Lean and Lean Six Sigma?
A great number of companies have implemented Lean principles and techniques, including Siemens, Lufthansa, Credit Suisse, Bombardier Transportation, and Opel in the manufacturing sector. Transactional and service companies have also applied Lean and Lean Six Sigma with success, benefiting from its time-saving, waste-removing and efficiency-gaining ways.
More examples of big-name companies that have employed Lean thinking and principles are Dell in optimizing demand-driven flow, eBay in bringing products and consumers together in real time and Microsoft in compressing its software development cycle. Healthcare concerns are implementing Lean too as they streamline the processes involved in patient care.
Why Lean Six Sigma?
Eliminate Waste, Decrease Lead Times, Increase Velocity, Reduce Variation, Achieve Near-Perfect Quality, and Lower Costs.
Companies typically use Lean to make immediate operational improvements as a direct output of "Kaizen events."
Staying competitive is sometimes the reason for preventing a long-term solution for elimination of the root cause for excess and obsolete inventory. Another reason may be the inability to unravel complex factors involved.
In the context of Performance Excellence, Lean principles and tools are most effectively employed when your intent is to make key, subordinate and enabling processes function as waste-free as possible. It is easiest for companies to undertake Lean after they have solidified their strategic direction, put a process architecture into place and aligned the business around that architecture.